Primus Line® technology is used for the trenchless rehabilitation of pressurised pipelines and for the construction of freely layable pipelines. Since the company was founded in 2001, Rädlinger primus line GmbH has professionalised the production of the flexible liner and the associated connectors to the highest quality standards. At the same time, the company has acquired a wealth of experience in the planning and realisation of pipeline projects through countless projects worldwide.
„We see ourselves not just as a technology supplier, but also as a comprehensive solution provider. Our aim is to ensure that our products are only used for suitable measures, that they are implemented reliably and that the pipelines can be operated permanently and safely."
Robert Goletz, Head of Technic Field
To achieve this goal, the company has two in-house civil engineering teams with a total of eight employees as well as another two-person team based in Pakistan. While the company installs the technology with its own construction site teams in Germany, it works with specially trained installation partners in other countries.
Robert Goletz and his colleagues support both their own construction projects and those of their partners. They train new installation partners and provide intensive support during the preparation and realisation of their first projects. In addition, the engineers work on projects that require a customised solution.
The technical departments are therefore closely involved in project management, but also take care of the basic technical documentation.
Engineering support for clients and partners
In the world of pipework technology, projects with flexible, fabric-reinforced liners have established themselves as an effective solution. Rädlinger primus line GmbH offers comprehensive technical support, starting with the initial discussions.
"We want to ensure that our product is suitable for the project and represents a safe solution," explains Robert Goletz. To do this, the engineers carry out a detailed feasibility study in advance. They analyse as-built plans, check application specifications and carry out inspections if necessary.
The precise planning of the measure includes, among other things, determining the diameter and pressure rating of the liners and connectors as well as testing the material resistance to the medium. The aim is to find an optimal, customised solution from an economic and technical point of view and to prepare cost-accurate quotations.
As part of further project management, the technical departments provide support in analysing the CCTV inspection (camera inspection), prepare reports and make recommendations for pipe cleaning. Hydraulic calculations on the properties of the pipes and implementation plans are also carried out in close consultation with the client. If required, special solutions can be developed and implemented in-house, while our own supervisors oversee the implementation of the measures on site.
In addition to the project, the client receives technical instructions for the long-term safe operation of his pipeline.
Leistungen im Überblick
- Documentation
- Installation manuals and guidelines
- Technical data sheets
- Process descriptions
- Tailored guidelines
- Project management
- Feasibility study and technical review
- CCTV inspection
- Hydraulic calculations
- Special solutions and troubleshooting
- Installation scheduling
- Supervision of the project
- Certification of partner companies
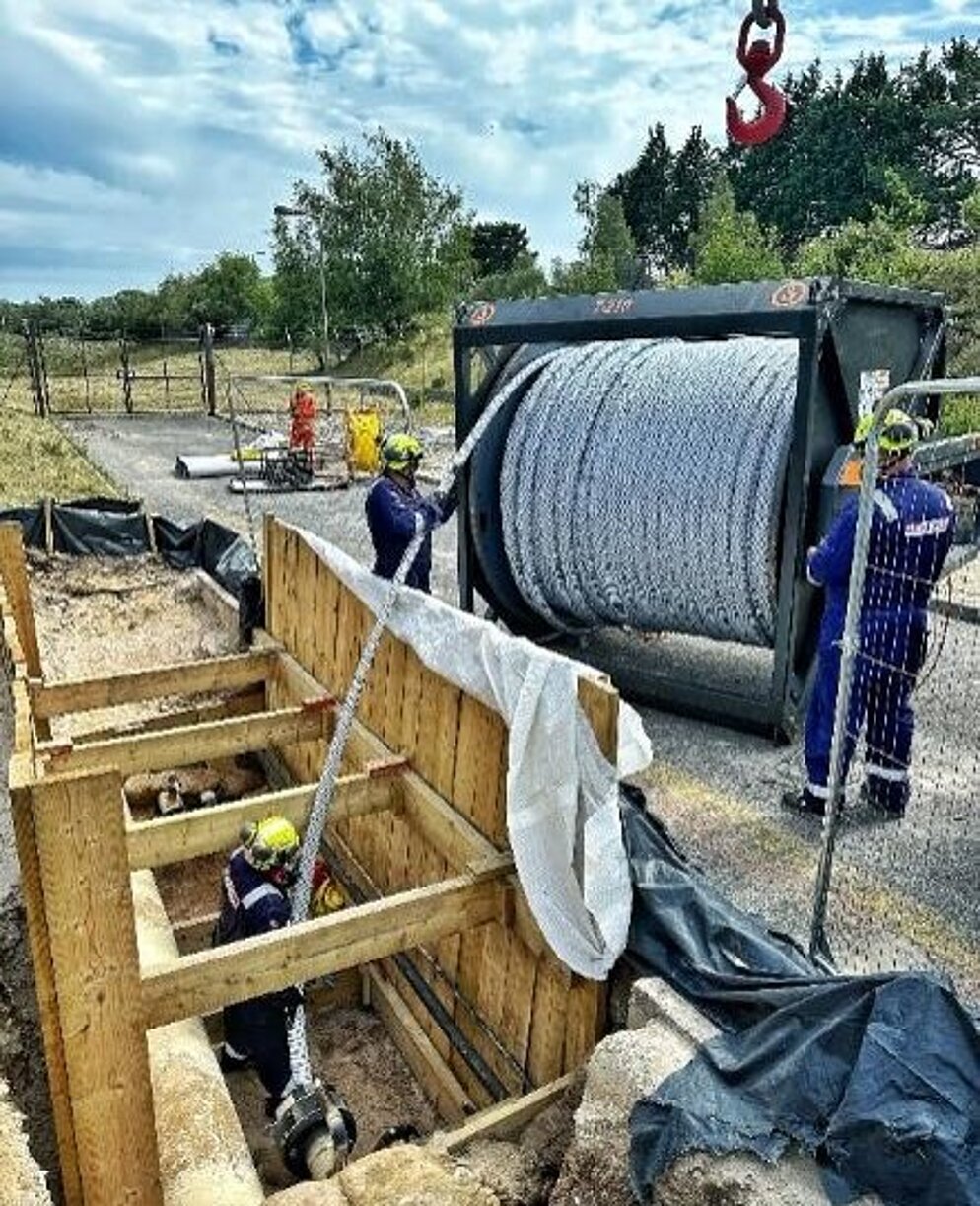
Customised solutions for a ten-kilometre-long pipeline
An outstanding example of the successful implementation of customised solutions is a project carried out by Primus Line partner Danphix S.p.A. from Italy in Wareham, southern England. A ten-kilometre-long pipeline with almost 200 bends for the extraction of hydrocarbons was renovated there trenchless.
The pipeline runs through a highly sensitive area with several nature and landscape conservation areas. An application for which Primus Line® is ideally suited due to its long installation lengths, low machine utilisation and bend flexibility.
As part of the project planning, the engineers from Rädlinger primus line GmbH checked the requirements for flow rate, operating temperature and pressure, among other things, and identified the Primus Line DN 150 medium-pressure liner for oil applications as a suitable rehabilitation solution.
During the implementation planning, the engineers paid particular attention to the number of installation sections and the location of the construction pits. The impact on the environment and the effects on tourism, flora and fauna were to be minimised as far as possible. The final planning envisaged eight sections with lengths between 200 and 2,382 metres.
In addition, special solutions were required for the connectors and the cable winch. The usual Primus Line connectors were out of the question due to the client's requirements. The solution was a modified connector consisting of three connector types, which met the requirements with a back flange, a temperature resistance of 60 degrees and a weld-on end. The usual winch with a steel cable was replaced by a winch with a flexible and lightweight HMPE cable so as not to jeopardise the integrity of the old pipe through friction when pulling it in.
The experience of Rädlinger primus line GmbH and the engineering support ensured the successful completion of the project.
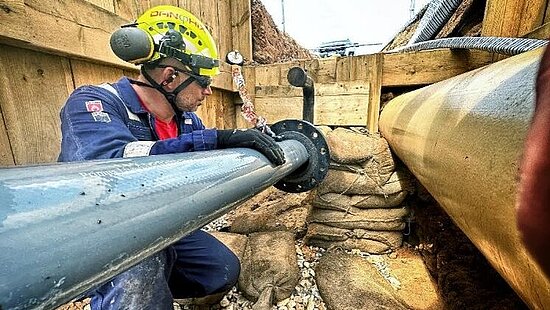
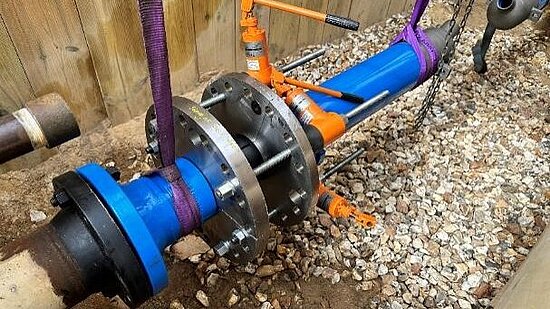