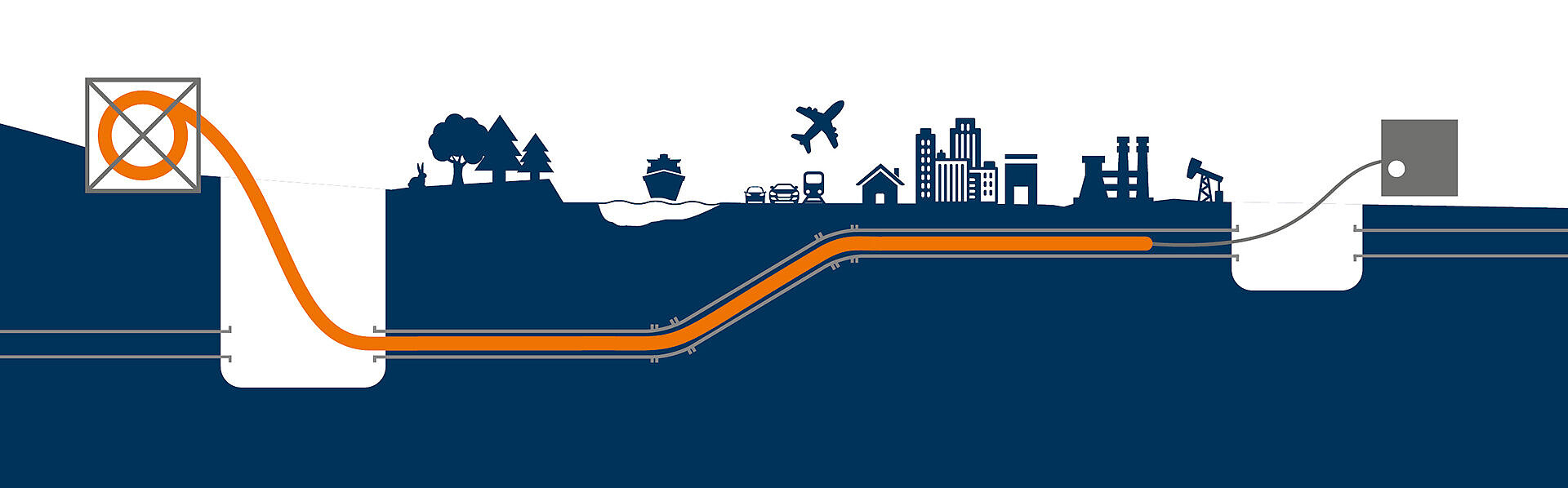
Installation process
Primus Line® is installed trenchlessly. This means: No more excavation pits with a length of several hundred metres of even several kilometres.
Two pits or existing shafts are sufficient for rehabilitating pressure pipelines. Here we explain how trenchless pipe rehabilitation with Primus Line® works.
Preparation
Creating the access
Small excavation pits or existing shaft structures: Primus Line® does not require more space for installation.
And only two of these are required per rehabilitation section. If the situation needs it – for example branches in the pipeline – additional intermediate pits are possible.
A cable winch is placed at the start and end pits for later work steps.
Decommissioning the pipeline
Before the rehabilitation work can begin, the pipeline must be taken out of service in accordance with the relevant regulations. It is at the discretion of the operator to set up a substitute supply.
Inspecting the host pipe
Deposits are not uncommon in old pipework. An accurate picture of the condition of the rehabilitation section is therefore immensly important for the successful installation of Primus Line®.
With their high-resolution cameras, long-range vehicle systems not only provide detailed images of the inside of the pipe, which are essential for precise preparation of the cleaning measures. They also pull in a pilot cable for the winches positioned at the start and end points.
Cleaning the host pipe
Tried and tested mechanical processes with spring steel scrapers and rubber discs reliably clean the pipes of encrusted deposits and foreign bodies – controlled by a second camera inspection.
This creates a free inner pipe diameter for the liner to be inserted.
Installation
Inserting the liner
Mounting the pulling head
For insertion, the liner is fitted with a pulling head designed for forces up to 100 kN. A twist catcher in the pulling connection to the cable winch prevents the liner from twisting on its way from the start pit to the destination pit.
Insertion and inflation
The liner is delivered folded. In this way, the installation of Primus Line® is even possible in pipes of the same nominal size.
Adhesive tapes hold the liner in this U-shape until it is pressurised with approximately 7.25 psi air pressure. It then changes to its round shape.
Mounting the connectors
The Primus Line connectors consist of a bushing and a core. Pressing the core into the press ring creates a tension-resistant unit of liner and connector: the flexible pipe. A solution with flange or welded end creates a force-fit connection with the host pipe.
Pressure test
The pressure test in accordance with relevant rules and regulations for liquid and gaseous media ensures the stability and especially leak-tightness of the section rehabilitated with Primus Line®. Specifically for water applications, the liner is additionally disinfected.
Reintegrating the rehabilitated pipeline
Installing a fitting piece
So that the pipeline can be put back into operation, a fitting is installed to reintegrate the rehabilitated section into the pressurised pipeline network.
Comprehensive documentation
The entire installation process is accompanied by detailed documentation – from inspection to pressure test. This ensures that the appropriate corrective measures can be taken quickly and in a targeted manner in the event of an emergency.