Since 2018, "Lining with inserted hoses" has already been listed in the international standard DIN EN ISO 11295 "Plastics piping systems used for the rehabilitation of pipelines – Classification and overview of strategic, tactical and operational activities".
This category includes a wide range of products and pipe types, including the Primus Line® technology reinforced with the para-aramid Kevlar®. The Primus Line pipe has a three-layer structure. The inner layer is adapted to the respective medium to be transported and, like the outer layer, is made of abrasion-resistant polyethylene (PE) or thermoplastic polyurethane (TPU). The outer layer protects the fabric in the middle from external influences during transport and installation.
The middle layer is the seamless aramid fabric. This layer absorbs any tensile forces and operating pressures without relying on the existing old pipe. For higher pressure levels in the medium and high-pressure range, only Kevlar® is used. The low-pressure system, on the other hand, consists of a hybrid fabric made of aramid and polyester for a cost-benefit-optimised and economical rehabilitation solution.
Other manufacturers do not reinforce their pipes with aramid and produce them exclusively on the basis of a pure polyester layer. "Basically, it can be said that aramid and polyester are two fundamentally different materials with different properties and consequently large differences in performance. This applies, for example, to strength, elongation and heat resistance," says Björn Bergmann, Head of R&D at Rädlinger primus line GmbH.
To understand the differences between aramid-reinforced and polyester pipes, it is particularly worth looking at the following mechanical properties of the two materials:
The modulus of elasticity (E-modulus) describes the relationship between stress and strain when a material is deformed. The higher the value, the greater the resistance that a material offers to its elastic deformation. For aramid, the value is approx. 70 to 100 gigapascals (GPa), for polyester approx. 3 to 15 GPa. The elongation at break indicates the maximum percentage elongation that a material will undergo at the moment of rupture. It therefore describes the deformability of a material under tensile load. This value is approx. 2 to 4 percent for aramid and approx. 15 to 25 percent for polyester. The breaking tenacity stands for the strength of the fibre/yarn and describes the amount of tensile stress a material can withstand before it fails. Aramid has a breaking tenacity of approx. 3 to 5 GPa, polyester a strength of 0.1 to 1 GPa.
This means that aramid has a higher strength in comparison. It expands less and breaks later, which has a positive effect on tensile strength, pressure resistance and service life. However, aramid pipes are still sufficiently flexible to allow for movement in the joints, ground movement, repair sections, step joints, lining through expansion joints, etc.
Aramid | Polyester | |
Modulus of elasticity | ~70 to 100 GPa | ~ 3 to 15 GPa |
Elongation at break | ~ 2 to 4 % | ~ 15 to 25 % |
Breaking tenacity | ~ 3 to 5 GPa | ~ 0.1 to 1 GPa |
The following qualitative advantages of the aramid-reinforced technology Primus Line® thus result from the material and manufacturing process:
Product tolerances and coating materials
The fabric of the Primus Line pipe is made from the aramid fibres with the help of a circular loom. The inner and outer layers are applied separately from both sides. This process allows different materials to be used for the inner and outer layers and enables a uniform wall thickness across the entire diameter.
Optoelectronic and optical measuring devices record all process parameters and allow continuous control of the tightly defined product tolerances with regard to the texture and wall thickness of the individual layers of the pipe.
Other suppliers produce the fabric first and then use an extrusion process to press the coating through the fabric to achieve a coating on both sides. This makes it impossible to use different materials for the inner and outer layers. Another consequence: uneven wall and layer thicknesses.
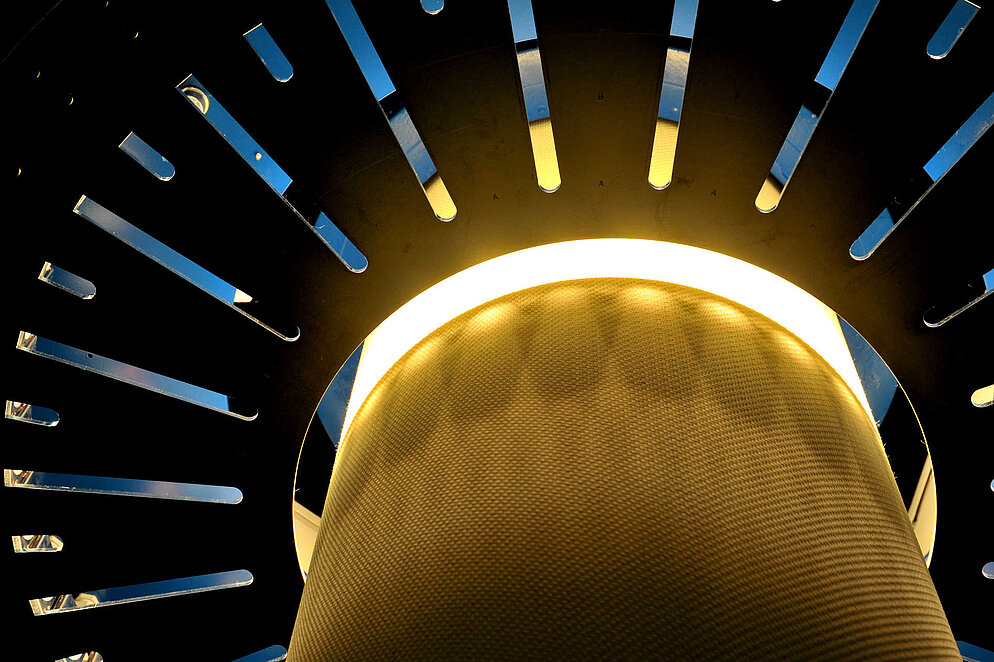
Installation lengths
The fabric-reinforced pipes are inserted into the existing pipeline with the help of winches. Longer installation lengths mean less disruption to the surrounding area, reduced downtime and rehabilitation period, and therefore help to determine the economic efficiency of a project.
The decisive factor for the installation length is, on the one hand, the breaking tenacity of the material. Since it is more pronounced for aramid than for polyester, aramid-reinforced pipes can withstand higher tensile forces. For the Primus Line® medium pressure system DN 150, for example, a maximum tensile force of 8.7 tonnes is permissible. Exceeding this would result in overstressing the material and may lead to long-term fatigue and failure of the pipe.
On the other hand, the elongation at break determines the installation length. The higher the elongation at break, the more the material stretches when pulled in. This means that polyester pipes stretch more under tension than aramid-reinforced pipes and are thus subject to higher tension. Bends or similar in the pipe can prevent this stress from being relieved even after insertion, which is why high pulling loads are already acting on the polyester pipe without the internal pressure load.
Depending on the existing bends in a pipeline, Primus Line® can realise insertion lengths of up to 2,500 metres in one section. The maximum possible installation length of polyester pipes is correspondingly lower.
Independence from the host pipe and maximum operating pressure
Due to the mechanical properties of the material, aramid-reinforced solutions such as Primus Line® are able to absorb the operating pressure of a pipe without using the support of the host pipe. An annular space remains between the host pipe and the inserted pipe. When pressurised, the Primus Line pipe retains its inner and outer diameters. Radial stresses are thus not transferred to the host pipe. The performance of the pipe, for example in terms of operating pressure, is therefore completely independent of the material, condition and state of the host pipe. On the contrary. Due to the transfer of internal pressure, the aramid-reinforced pipe even reduces the load on the host pipe and thus extends its service life at the same time.
Due to the high E-modulus, even high operating pressures can be achieved with absolute reliability. The Primus Line® medium pressure system DN 150, for example, allows operating pressures of up to 56 bar on the straight line. This is verified by burs pressure tests on each production batch, in which a section of exposed or unobstructed pipe with suitable connectors is subjected to water until it bursts.
In comparison, the polyester hose expands much more under pressure load and will lean against the host pipe. This is due to the lower modulus of elasticity (E-modulus) and the simultaneously higher elongation at break of polyester.
The maximum pressure load capacity of a pipeline rehabilitated with a polyester pipe thus also depends on the individual strength of the host pipe material and the general condition of the pipeline. Corrosion holes, breaks and cracks weaken the strength of the host pipe and provide insufficient support for the polyester pipe. Bends, repair sections, step joints and lining through expansion joints are also unsupported areas. The stresses acting on the host pipe here pose risks to the host and the inserted pipe. As a result, the ageing process of the pipe continues and increases the probability of failure.
The maximum possible operating pressure of a pipe rehabilitated with a polyester pipe is therefore more difficult to calculate. Such risks can be avoided with aramid-reinforced pipes.
Bendability
Since the polyester pipe needs the support of the host pipe to achieve the operating pressure, it must also fit the host pipe in bends. To attain this, bends are limited toa maximum of 30 degrees and the operating pressure must be reduced as overloading by internal pressure would lead to premature fatigue and finally to a failure of the pipe.
Despite the high modulus of elasticity of aramid, the Primus Line pipe is flexible so that the system can pass bends of up to 90 degrees. However, due to the compression or expansion of the material in bends, a loss of performance, e.g. in terms of maximum operating pressure, must be expected. This is taken into account at the project planning stage and included in the product selection.
Service life
Primus Line® extends the service life of a pipe by at least another 50 years. This is the result of various long-term tests of the pipe, ranging from 100 to 10,000 hours, carried out as part of DVGW and API certification in accordance with ISO and ASTM standards. Again, the material is crucial, because while aramid has a creep rate of about 0.035 percent per decade, polyester deforms almost six times as fast, with a creep rate of about 0.2 percent. As a result, polyester pipes age faster.
What is aramid?
The term aramid is an abbreviation of the two words "aromatic polyamides". A distinction is made between the two main types of aramids: para-aramid and meta-aramid. While para-aramid is characterised by high strength, meta-aramid stands for heat and flame resistance. The golden-yellow organic material is usually produced in the form of fibres. Compared to polyester, aramid fibres have, among other things, higher toughness, low elongation and a high melting point of about 450 degrees. The fibres were developed by DuPont in 1965. Different manufacturers call aramid by different trade names such as Kevlar from DuPont, Twaron and Technora from Teijin in Japan or Arawin from Toray in Korea.